CNC Lathe Machine Parts Factory: Revolutionizing Metal Fabrication
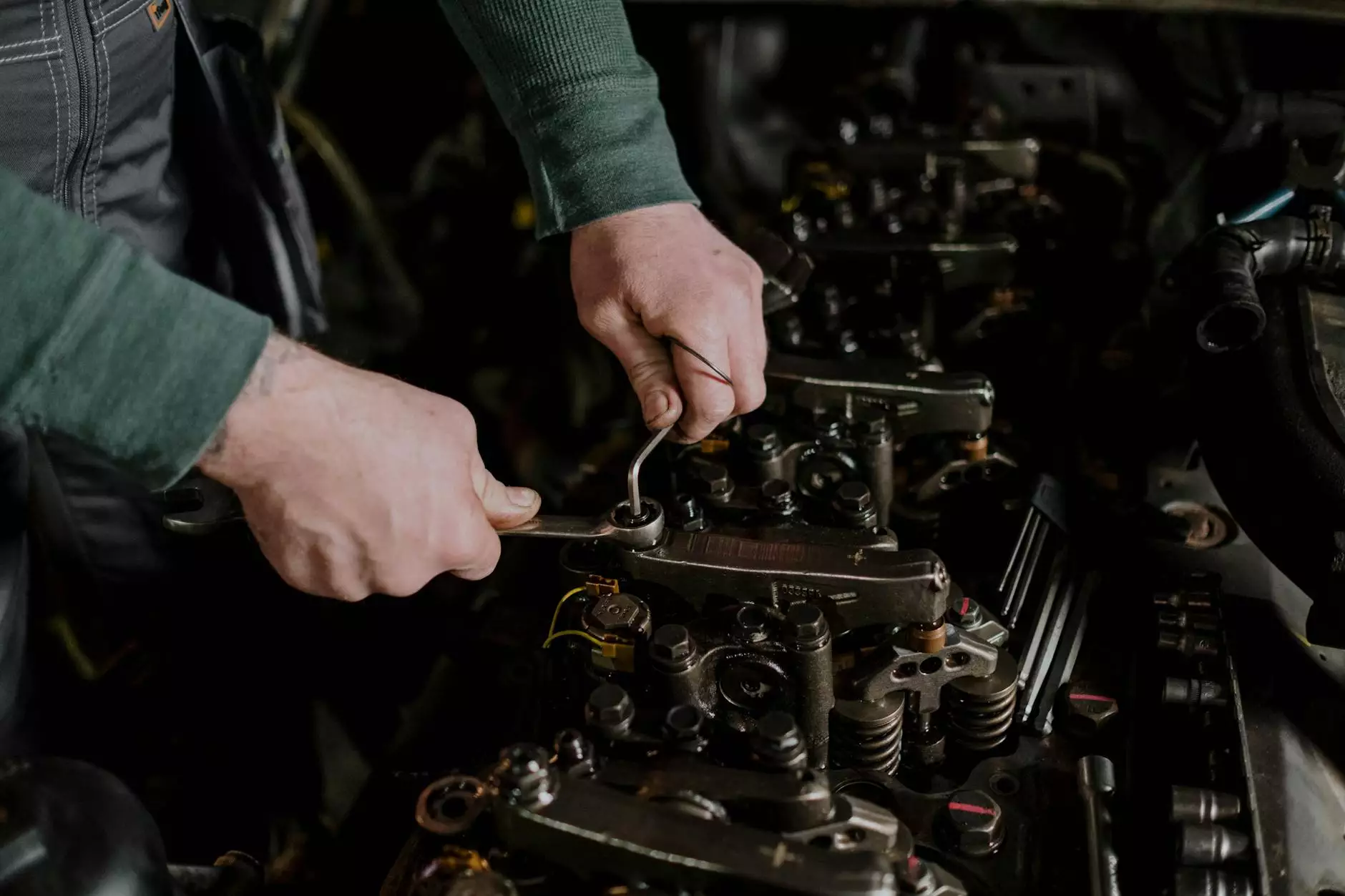
The advancement of technology has dramatically altered the landscape of the manufacturing industry. Among these technological marvels are CNC (Computer Numerical Control) machines, specifically cnc lathe machines. These machines have become a cornerstone in the realm of precision engineering and metal fabrication. In this article, we delve deeply into the workings of a cnc lathe machine parts factory, exploring its processes, advantages, and the future it holds for the industry.
Understanding CNC Lathe Machines
CNC lathe machines are essential tools in the manufacturing sector, known for their precision and efficiency. They operate by rotating a workpiece against cutting tools to shape material into desired forms. This process is integral for creating a wide range of products, from simple components to complex engineered parts.
The Basics of CNC Technology
- Computer Numerical Control (CNC): CNC technology allows machines to be controlled by computers, leading to improved accuracy and efficiency.
- Automation: CNC lathes operate with minimal human intervention, reducing the likelihood of errors and improving production speed.
- Versatility: These machines can handle various materials—metal, plastic, wood—making them invaluable in multiple industries.
Benefits of Utilizing a CNC Lathe Machine Parts Factory
Investing in a cnc lathe machine parts factory offers numerous benefits that can significantly impact a business’s operational efficiency and output quality. Some of these benefits include:
1. Precision Manufacturing
The primary advantage of using CNC lathes is their ability to create highly precise components. This precision ensures that each part meets stringent specifications, reducing waste and rework.
2. Increased Efficiency
With CNC technology, manufacturers can produce parts faster than traditional methods. The automation of processes leads to a significant reduction in lead times, allowing for quicker order fulfillment.
3. Flexibility in Production
CNC lathes can be programmed for different products without significant downtime. This flexibility helps manufacturers adapt to changing market demand and customer specifications. Whether it's small batch production or large-scale manufacturing, a cnc lathe machine parts factory can accommodate various orders effectively.
4. Lower Labor Costs
Automation reduces the need for extensive manual labor, allowing companies to streamline their workforce and reduce operational costs. While skilled operators are still needed, the overall labor expense can be significantly lower.
5. Improved Safety
By minimizing human intervention in potentially hazardous processes, CNC machines improve workplace safety. Operators can program the machines from a safe distance, reducing the risk of injuries associated with manual machining.
The Role of a CNC Lathe Machine Parts Factory
In a cnc lathe machine parts factory, the production process involves several critical steps that ensure the manufacturing of high-quality components. Understanding this workflow can provide insights into the operational capabilities of such factories.
1. Prototyping and Design
The first step in the production process is prototyping and design. Engineers use CAD (Computer-Aided Design) software to create detailed models of the components. This stage is crucial, as a well-designed prototype reduces errors in later stages.
2. Programming
Once the design is finalized, the next step is programming the CNC lathe. Operators use CAM (Computer-Aided Manufacturing) software to convert the CAD design into a machine-readable format, dictating how the CNC machine will operate.
3. Setup
The setup phase involves preparing the CNC lathe machine, including the installation of necessary tools and loading the material onto the machine platform. Proper setup is vital for ensuring that the manufacturing process runs smoothly.
4. Machining Process
During the machining process, the CNC lathe operates according to the programmed instructions. The machine rotates the workpiece while cutting tools shape it as per the specifications. This stage is where precision and efficiency come together.
5. Quality Control
Quality control is an integral part of manufacturing in a cnc lathe machine parts factory. After machining, parts undergo thorough inspection to ensure they meet quality standards. Methods such as dimensional inspection, surface finish analysis, and functional testing are routinely employed.
6. Finishing
After successfully passing quality control, parts may go through additional finishing processes such as deburring, polishing, or coating. These processes enhance the durability and visual appeal of the components.
Applications of CNC Lathe Machine Parts
CNC lathe machines produce components that are utilized across various sectors. Here are some industry applications:
- Aerospace: Precision machined parts for engines, landing gear, and structural components.
- Automotive: Manufacturing of engine components, transmission parts, and specialized fittings.
- Medical: Production of surgical instruments, prosthetics, and medical device components.
- Electronics: Creation of housing, connectors, and mechanical parts for electronic devices.
- Construction: Fabrication of fittings, brackets, and other essential construction components.
The Future of CNC Lathe Machine Parts Factories
The future of cnc lathe machine parts factories is bright, with continual technological advancements and growing industry demands. Here are some trends shaping the future:
1. Industry 4.0 Integration
The merging of Internet of Things (IoT) technology with manufacturing processes is a key trend. Smart machines equipped with sensors can communicate operational data, enhancing monitoring, predictive maintenance, and efficiency.
2. Sustainable Manufacturing
As global concern for the environment grows, manufacturers are adopting sustainable practices. This includes using recycled materials, implementing energy-efficient processes, and reducing waste. CNC technology allows for more precise material usage, contributing to sustainability efforts.
3. Advanced Materials
The discovery and utilization of new materials like composites and high-strength alloys are expanding the scope of what CNC lathe machines can create. Factories that invest in adapting to these materials will have a competitive edge.
Why DeepMould.net Stands Out
At DeepMould.net, we pride ourselves on being a leading name in the metal fabrication industry. Our cnc lathe machine parts factory incorporates cutting-edge technology, skilled labor, and a commitment to quality. Here’s why we stand out:
- Expertise: With years of experience in the industry, our team understands the nuances of precision machining.
- Quality Assurance: We leave no stone unturned when it comes to quality. Our rigorous quality control processes ensure top-notch products.
- Customer-Centric Approach: We work closely with our clients to understand their unique needs and tailor our services accordingly.
- Innovation: Constantly evolving, we embrace new technologies and methodologies to stay at the forefront of the industry.
In conclusion, the realm of cnc lathe machine parts factories is not just about manufacturing; it is about innovation, precision, and meeting the evolving demands of modern industries. As technology continues to advance and industries grow, CNC lathes will play an increasingly vital role in ensuring high-quality production across various sectors.
If you are looking for a trusted partner in the world of CNC machining, consider DeepMould.net. Our commitment to excellence and customer satisfaction makes us the ideal choice for your manufacturing needs.