The Excellence of China Molds: A Deep Dive into Plastic Mold Making
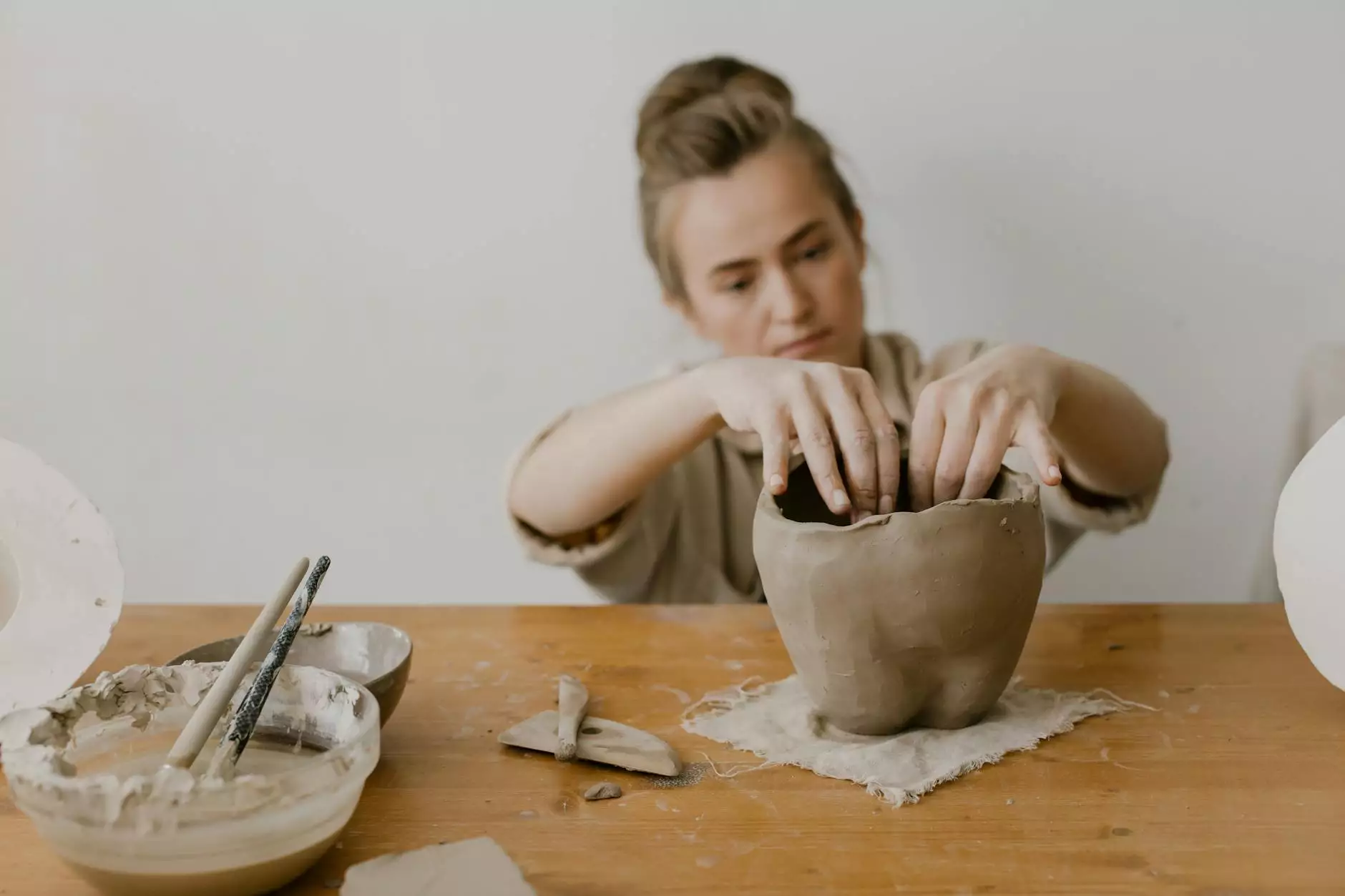
The landscape of manufacturing has evolved remarkably over the years. As we stand at the forefront of an industrial revolution, the emphasis on quality and efficiency has never been greater. Among the many innovations driving this shift, China molds have emerged as a vital component in the plastic molding industry. This article will explore the essential aspects of plastic mold making and the significance of China molds in today’s global market.
The Significance of Plastic Molds in Modern Manufacturing
Plastic molds are an integral part of various manufacturing processes, particularly in the production of consumer goods, automotive parts, medical devices, and more. The importance of molds lies in their ability to shape materials into desired forms with precision and repeatability. Here are some key reasons why plastic molds are crucial:
- Efficiency: Molds allow for mass production of identical parts, significantly speeding up the manufacturing process.
- Cost-Effectiveness: Once a mold is created, additional parts can be produced at a lower cost compared to many other manufacturing methods.
- Design Flexibility: Molds can be designed to create intricate shapes and designs that would be impossible to achieve using traditional methods.
- Material Versatility: China molds can work with a variety of plastics, allowing manufacturers to select the material best suited for their application.
Understanding the Different Types of Plastic Molds
In the realm of plastic mold making, there are several types to consider, each with its specific applications and advantages:
1. Injection Molds
Injection molds are among the most commonly used type of molds. In this process, melted plastic is injected into a mold cavity under high pressure. After cooling, the mold opens, and the part is ejected. This method is optimal for high-volume production due to its speed and precision.
2. Blow Molds
Blow molding is primarily used for creating hollow plastic objects. Polyethylene bottles and containers are often produced using this technique. The process involves inflating hot plastic inside a mold, which then cools to form the desired shape.
3. Compression Molds
Compression molding is suitable for larger parts, such as automotive components. In this method, plastic resin is placed in a heated mold, where it is compressed to form the desired shape through heat and pressure.
4. Rotational Molds
Rotational molding is perfect for creating large, hollow, and seamless plastic items. As the mold rotates, the plastic is dispersed and covers the inner walls, producing highly durable products often used in playground equipment and storage tanks.
The Process of Plastic Mold Making in China
China has established a reputation as a leading manufacturer of plastic molds. The process of mold making typically involves the following steps:
1. Design and Engineering
The journey begins with design. Skilled engineers and designers use advanced software to create detailed CAD (Computer-Aided Design) models. These designs dictate the exact specifications of the mold, including dimensions, cavities, and features.
2. Material Selection
The choice of material is crucial for the durability and functionality of the mold. Common materials include steel and aluminum, each offering unique benefits. China molds manufacturers often opt for high-quality steel to ensure longevity, especially for high-volume production runs.
3. Machining and Fabrication
Once the design is finalized, the fabrication process begins. Utilizing CNC (Computer Numerical Control) machining, precise cuts and shapes are created based on the design. This step is critical, as any inaccuracies can lead to defects in the final product.
4. Assembly and Testing
After machining, the individual components of the mold are assembled. Quality checks are conducted to ensure that every part fits perfectly and functions as intended. Testing is often performed using trial runs to ensure that the mold produces parts that meet quality standards.
5. Production and Quality Assurance
Once the mold passes testing, it is ready for mass production. Continuous quality assurance checks are carried out to ensure that every part produced meets the exact specifications and quality standards required by clients.
Advantages of Sourcing Plastic Molds from China
Choosing to source plastic molds from China comes with a myriad of benefits:
1. Competitive Pricing
One of the most significant advantages is the competitive pricing. Due to lower labor costs and a vast manufacturing infrastructure, companies can save substantially on mold production.
2. High-Quality Standards
Despite the low costs, Chinese manufacturers often adhere to high-quality production standards. Many factories are ISO-certified, ensuring that they meet international quality requirements.
3. Cutting-Edge Technology
Chinese mold manufacturers invest heavily in state-of-the-art technologies and machinery. This investment allows for the production of complex molds with precision and efficiency.
4. Quick Turnaround Times
Given their extensive experience and streamlined processes, manufacturers in China can produce molds relatively quickly. This speed can significantly accelerate time-to-market for new products.
5. A Wide Range of Services
Many Chinese mold makers offer comprehensive services that go beyond just mold making. They often provide product design assistance, prototyping, and even production services, making them a one-stop solution for businesses.
Choosing the Right Plastic Mold Manufacturer in China
When it comes to selecting a plastic mold manufacturer in China, there are several factors to consider:
- Experience: Look for manufacturers with a proven track record in the industry, particularly in your specific area of need.
- Technical Capabilities: Ensure that the manufacturer possesses the necessary technology and equipment to meet your requirements.
- Quality Assurance Processes: Inquire about their quality control measures and certifications to guarantee product quality.
- Communication: Effective communication is key to a successful partnership. Choose manufacturers who understand your requirements and can provide regular updates.
- Customer Reviews: Research customer feedback and testimonials to understand the experiences of others who have worked with the manufacturer.
The Future of Plastic Molds in Industry
As industries evolve, so does the technology and methodology related to plastic molds. The future promises innovations such as:
1. Automation and AI
Advancements in automation and artificial intelligence are expected to enhance the efficiency and accuracy of mold production. Predictive maintenance and automated quality checks can further optimize manufacturing processes.
2. Sustainable Practices
As environmental concerns rise, more manufacturers are adopting sustainable practices. The use of eco-friendly materials and recycling processes will become more prevalent in mold manufacturing.
3. Customization
The demand for personalized products is rising. Future production techniques may allow for more customizable mold designs, enabling businesses to respond swiftly to market trends.
Conclusion: Embracing the Power of China Molds
In conclusion, China molds represent a cornerstone of modern manufacturing, delivering quality, efficiency, and cost-effectiveness. With an array of benefits, including technological advancements and competitive pricing, sourcing your plastic molds from China can be a strategic decision for any business looking to enhance their production capabilities. As we look toward the future, the continuous evolution of mold making promises exciting opportunities for innovation and growth.
By choosing the right manufacturer and embracing ongoing advancements in the industry, businesses can harness the full potential of plastic molds to propel their products to new heights. Explore your options with top providers like Hanking Mould to discover how they can support your manufacturing needs.