CNC Machined Parts Manufacturers: Excellence in Precision Engineering
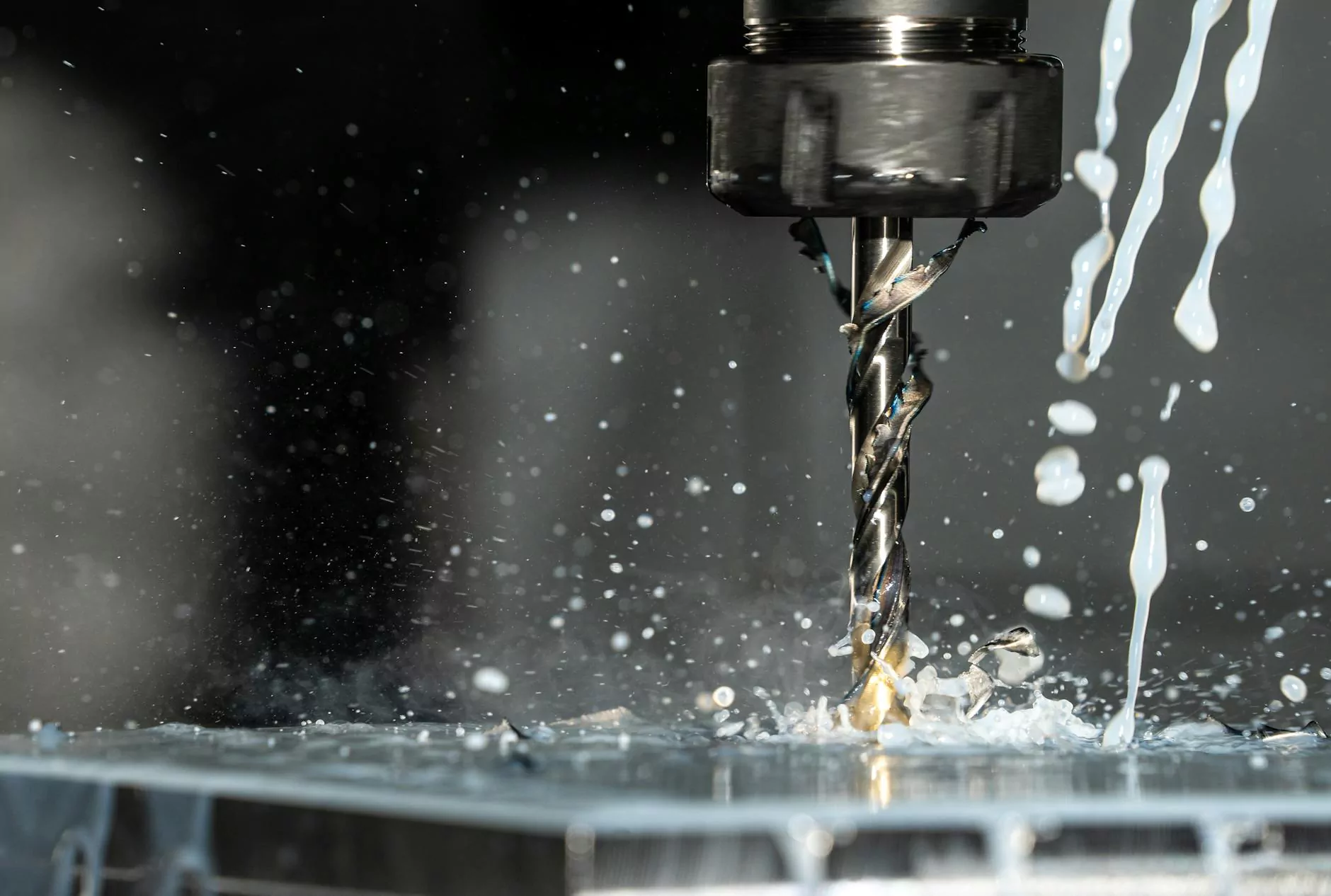
The world of cnc machined parts manufacturers is a testament to technological advancements and engineering excellence. As industries evolve, the demand for precision-engineered components continues to soar. This article delves deep into the various aspects of CNC machining, laser cutting, welding, plastic injection, vulcanization, and the indispensable role of industrial supplies in manufacturing high-quality components. Prepare to discover the intricate details that make these processes fundamental to modern manufacturing.
Understanding CNC Machining
CNC machining, or Computer Numerical Control machining, is at the forefront of precision engineering. It utilizes computer technology to control machine tools and produce highly accurate components. This process stands out due to its ability to create complex shapes and geometries that manual machines could never achieve.
Advantages of CNC Machining
- Precision: CNC machines can achieve tolerances as tight as ±0.001 inches, ensuring that every part is produced to exact specifications.
- Consistency: Once a design has been programmed, CNC machines can replicate the same part consistently, making them ideal for large-scale production.
- Flexibility: CNC systems can be reprogrammed and adapted for various tasks, allowing manufacturers to pivot quickly to market demands.
- Reduced Waste: Advanced software optimizes cutting processes, minimizing material waste and enhancing cost-efficiency.
Laser Cutting: A Game Changer in Manufacturing
Laser cutting is another pivotal technology employed by cnc machined parts manufacturers. This process uses high-powered lasers to cut and engrave materials with remarkable accuracy. The ability to cut through various materials—metal, plastic, wood, and more—has revolutionized how parts are fabricated.
Key Features of Laser Cutting
- High Precision: Laser cutting provides clean, accurate cuts that require little to no finishing.
- Speed: The speed of laser cutting machines significantly reduces lead times in production.
- Versatility: Their capability to work with a broad range of materials makes laser cutting a versatile option for manufacturers.
- Minimal Material Deformation: The focused heat of the laser minimizes the heat-affected zone, reducing warping or other material deformation.
Welding Technologies in CNC Manufacturing
Welding is an essential process that joins materials, typically metals or thermoplastics, by melting them at their joining points. CNC machined parts manufacturers often rely on various welding techniques to ensure assembly integrity and durability.
Types of Welding in Manufacturing
- MIG Welding: Metal Inert Gas welding is popular for its speed and versatility in welding different types of metals.
- TIG Welding: Tungsten Inert Gas welding is known for its precision and ability to weld thin materials.
- Spot Welding: A very efficient method for joining sheets of metal, commonly used in automotive manufacturing.
- Laser Welding: Integrating laser technology with traditional welding processes enhances precision and reduces thermal distortion.
Plastic Injection Molding for Precision Parts
Plastic injection molding is a manufacturing process that involves injecting molten plastic into a mold to create intricate shapes and components. This method is particularly important for producing high-volume, complex parts used in various industries.
Benefits of Plastic Injection Molding
- Efficiency: High-speed production capabilities make it perfect for large runs of consistent parts.
- Detail and Design: Injection molding can produce highly detailed and complex geometries that would be impossible with other methods.
- Material Variety: A wide array of plastic materials can be utilized, allowing manufacturers to choose the best material for their specific applications.
- Cost-Effective: Although the initial setup may be costly, the overall production cost decreases significantly with high-volume output.
Vulcanization: Strengthening Materials
Vulcanization is a chemical process that involves treating rubber with sulfur to improve its properties, making it more durable and elastic. This process is crucial for industries that rely on rubber components in their products, such as automotive and consumer goods.
Significance of Vulcanization
- Enhanced Durability: Vulcanized rubber withstands wear, heat, and chemicals better than untreated rubber.
- Improved Elasticity: The process significantly improves the material's elasticity and tensile strength.
- Resistance to Environmental Factors: Vulcanized materials demonstrate better resistance to UV light, ozone, and extreme temperatures.
Industrial Supplies: The Backbone of Manufacturing
The success of cnc machined parts manufacturers is heavily reliant on quality industrial supplies. These supplies include raw materials, tools, and components essential for the manufacturing process. Dependable suppliers ensure that manufacturers have everything they need to produce high-quality parts efficiently.
Importance of Reliable Industrial Supplies
- Quality Assurance: Reliable suppliers provide high-quality materials that meet industry standards, ensuring the final products are safe and effective.
- Timely Delivery: Establishing strong relationships with industrial supply companies ensures timely delivery, keeping production schedules on track.
- Cost Management: Bulk purchasing and long-term supplier contracts can help mitigate costs, enhancing overall profitability.
- Technical Support: Many reputable suppliers offer technical support, helping manufacturers solve issues and optimize production processes.
The Future of CNC Machining and Manufacturing
The landscape of CNC machining and manufacturing is continuously evolving. With advancements in technology, the future looks promising and filled with innovations. From the integration of AI and machine learning to improvements in robotics and automation, manufacturers are poised to enhance their production capabilities further.
Innovations Shaping the Future
- Additive Manufacturing: Combining CNC machining with 3D printing technologies can lead to new hybrid processes, expanding design capabilities.
- Smart Manufacturing: The Internet of Things (IoT) is ushering in intelligent manufacturing systems that can predict maintenance needs and optimize processes.
- Sustainable Practices: As industries face increasing pressure to adopt eco-friendly practices, developments in sustainable materials and processes will play a critical role.
- Advanced Automation: Automation technologies will continue to advance, allowing for greater efficiency, accuracy, and productivity in manufacturing.
Conclusion
In summary, the expertise and capabilities of cnc machined parts manufacturers are foundational to numerous industries. Through advancements in machining, laser cutting, welding, plastic injection, and the consistent availability of quality industrial supplies, these manufacturers are equipped to meet tomorrow’s challenges with confidence. As technology continues to evolve, those who embrace these changes will undoubtedly find themselves at the forefront of the manufacturing sector.
For more information about CNC machining and how your projects can benefit from these technologies, feel free to visit sumiparts.us for expert guidance and quality service tailored to your manufacturing needs.